Operating Hours Explorer – tool to determine exact operating hours of spare parts
- Sep 12, 2022
- 2 min read
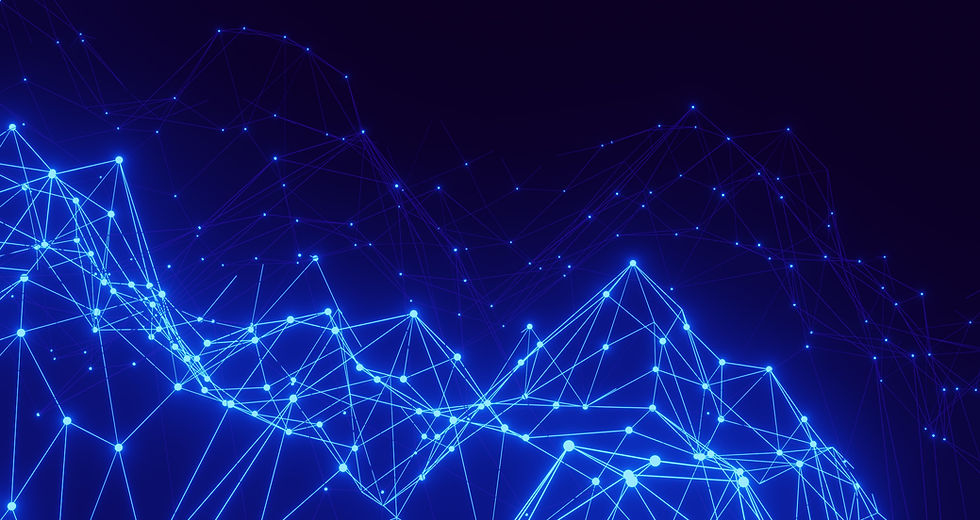
In complex manufacturing plants, predictable maintenance by accurately recording the operating hours of each spare part has not been possible until now. For this purpose, Quantis has developed and launched the Operating Hours Explorer. With this tool, it is possible to precisely determine the operating hours of spare parts with predictive maintenance, and significantly increase their service life.
Using the example of filling valves in the beverage filling industry, we will show how the Operating Hours Explorer works.
Initial situation Up to now, maintenance in a bottling plant was carried out on an annual basis. Days of maintenance with resulting machine downtimes are very expensive for companies. All filling valves are removed, serviced and, if necessary, replaced. The valves are replaced according to the operating hours specified by the OEM.
What was done In the Operating Hours Explorer, the Maintenance Manager records the operating status, the last general overhaul and the associated operating hour durations for each filling valve. As a rule, the OEM specifies an operating hour duration of 6,000 hours. The Operating Hours Explorer uses an automated learning process to determine the actual service life (operating hours benchmark) of a filling valve. In addition, the tool uses predictive maintenance to monitor the states of the filling valves to predict when which valve should be replaced. Defined parameters provide the data basis for visual representations of the valves' status. The display is done in a dashboard (in this case a heat map), which allows the user to easily see changes in the valves.
Results The plant operator was able to almost double the operating hours of the filling valves with this method! This saves enormous costs in the procurement of spare parts. In addition, the Operating Hours Explorer provides an overview of spare parts that actually need to be replaced. In this way, spare parts can be used beyond the benchmarks. In the event of premature wear, a warning is given in good time so that the valve in question can be replaced quickly and easily without significantly disrupting the production process.
Operating hours can be recorded
Monitoring of the operating hours of spare parts
Correct mapping of operating hours (automated benchmark determination)
Plannable maintenance thanks to accurate recording of operating hours
Picture by Unsplash
Comentários